PROCESS
Duferco Danish Steel is part of the steel division of Duferco Group, major international player within trading and processing of steel.
THE PROCESS
Billet’s Furnace
Our furnace is a pusher type reheating furnace, heated by the natural gas, with 3 zones of regulation, temperature 1160°C – 1275°C. The billets stay in the furnace approximately for 2 hours. The production tempo is approximately 70 tons/hours.
The billets are heated to the rolling temperature (average billet temperature 1135°C).
The following parameters, which influences the product quality are measured and registered:
- Furnace temperature in Zone 1, Zone 2 and Zone 3
- Billet temperature in Zone 3, at the descaler, in the rolling stand 7 and after the last rolling stand
- Cooling water for the rolling stands
- Temperature of the combustion gases
- The pressure and the content of oxygen in the furnace atmosphere
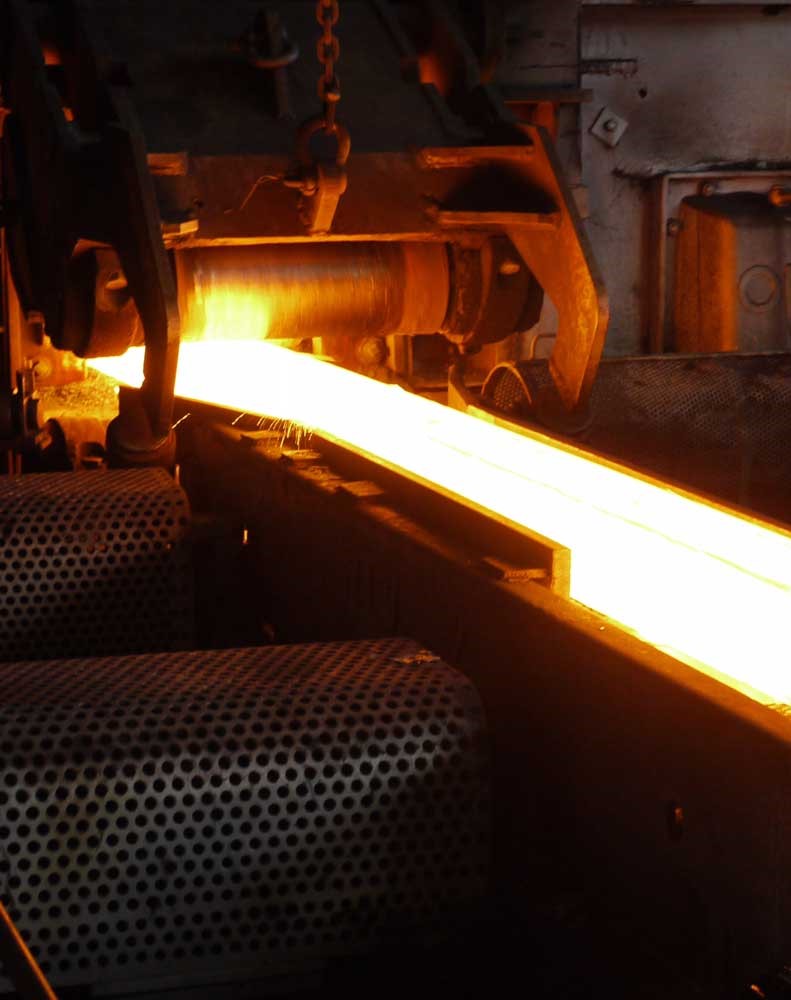
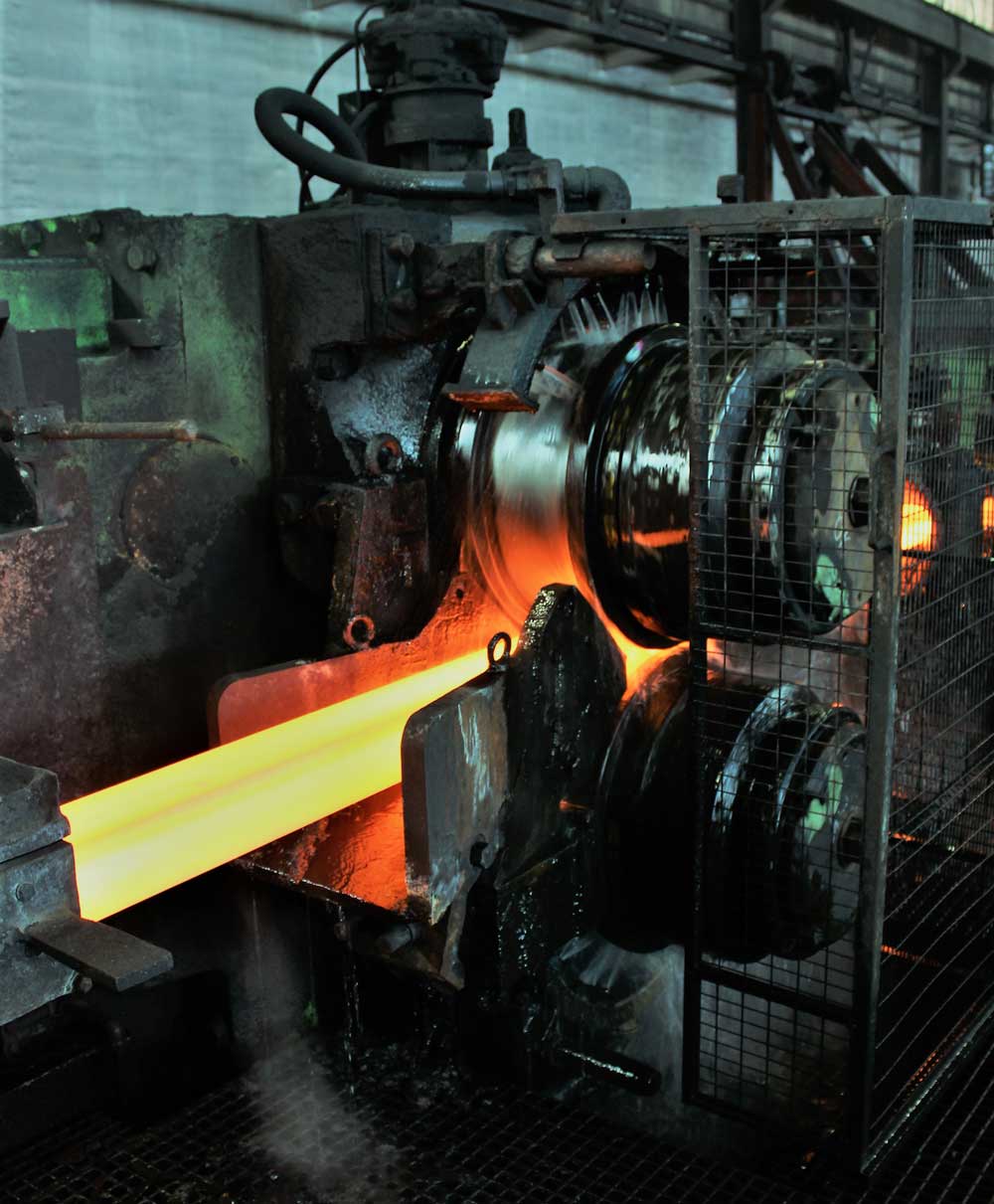
Descaller
The billets are pushed out of the furnace and conveyed via the roller table through the descaler, where the scale is removed from the surface by using the high pressure water (up to 250 bars). Afterwards the billets are led into the first rolling stand.
The following parameters, which influence the product quality are observed:
- The function of the descaler is checked by visual control
- Adjustment of the water pressure of the descaler
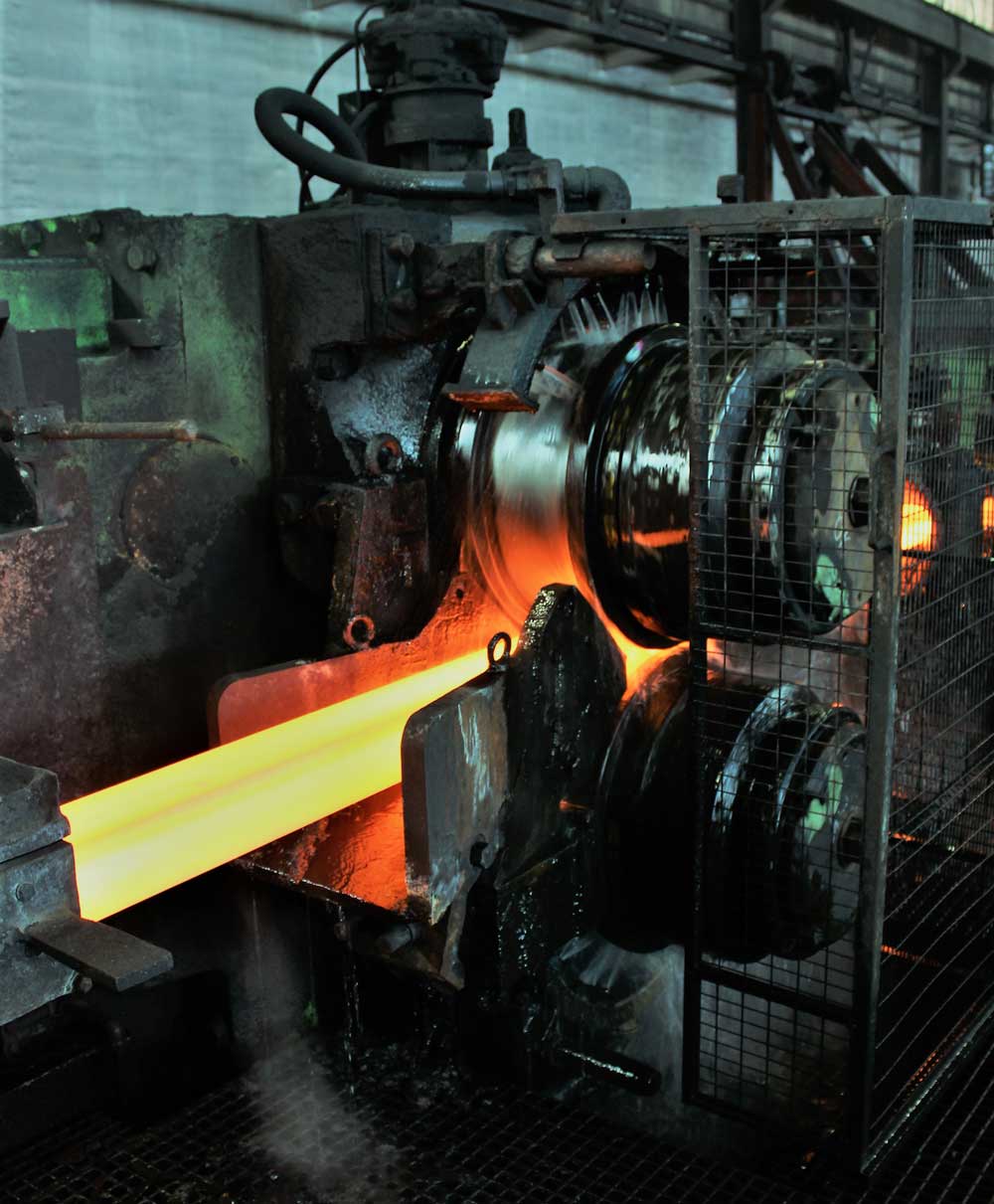
Rolling
Hot rolling of the billets to final dimensions. Average productivity is between 50-70 t/h depending on the dimensions. The billets are led through the roughing, the intermediate and the finishing train, which consist of up to 19 horizontal and vertical rolling stands in one continuous line. The number of rolling stands, which are used, depends of the form and the dimensions of the finished product. After the last rolling stand, a shear cuts the rolled material in lengths for the cooling bed.
The following parameters which influence the quality of the product are observed:
- Tension between the rolling stands
- Temperature before the rolling stand 7
- Control of the dimensions after the last stand by optic gauge
- Control of the dimensions of rolled material between the rolling stands
- Adjustment of the cooling water for the rolling stands
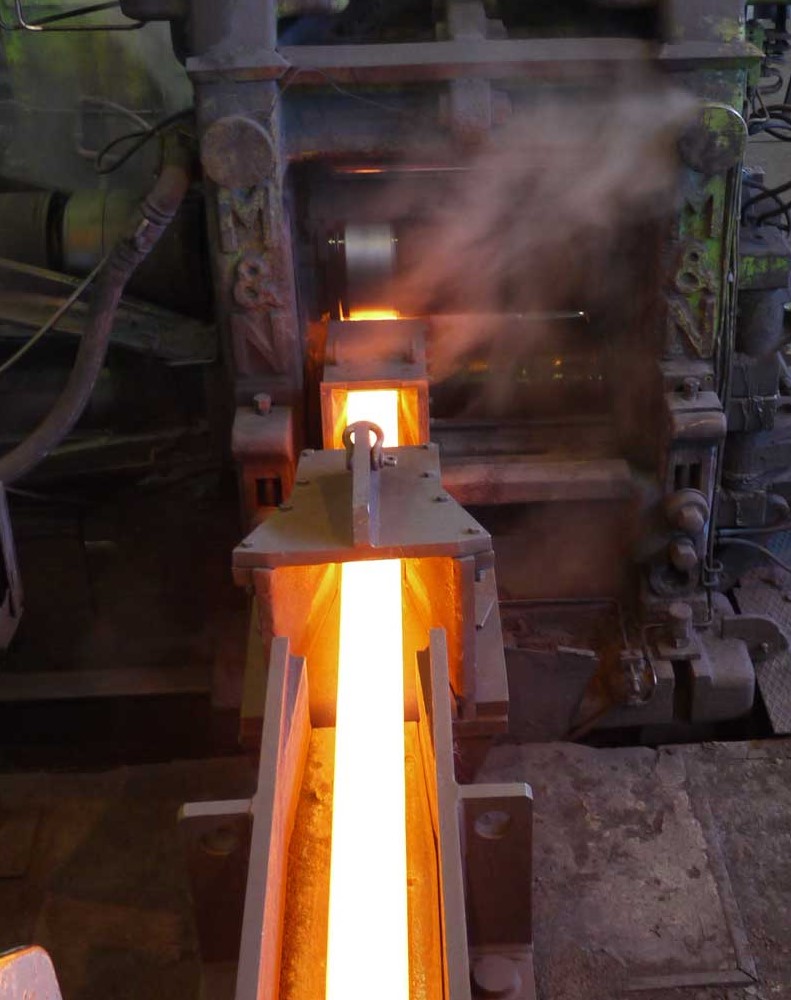
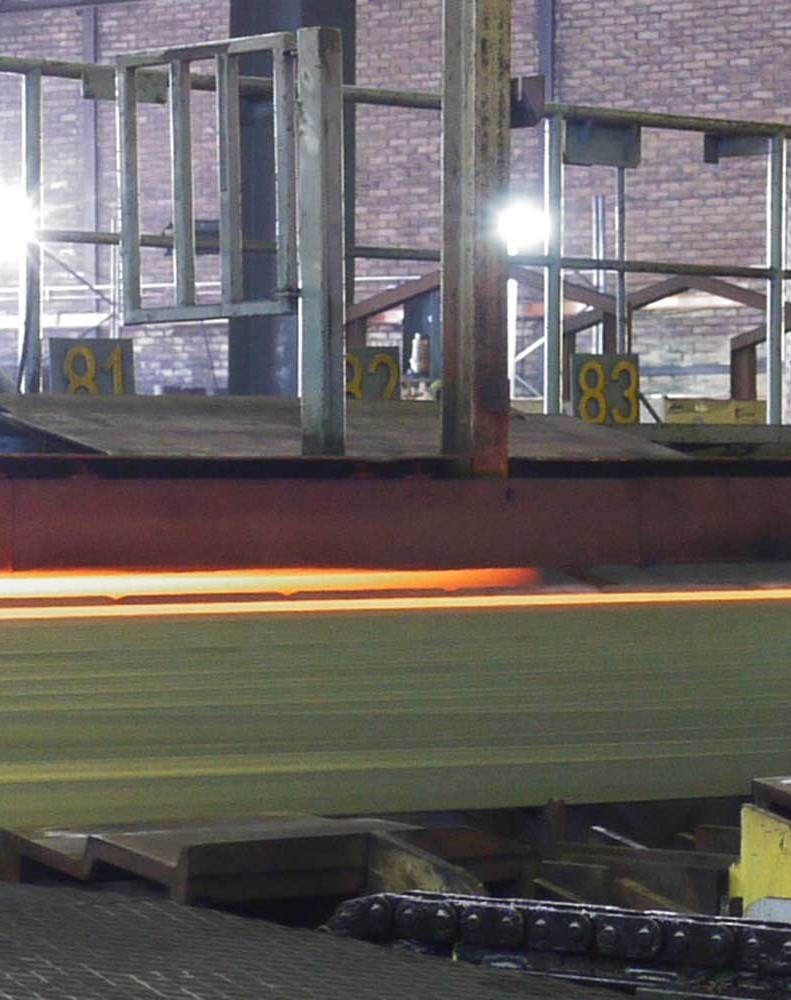
Cooling Bed
Air cooling of the hot rolled flat, square and round bars. Equal angles and channels (U-steel) are straightened in a straightening machine in-line.
Samples are taken from the cooling bed for control of the following parameters which are measured and registered:
- dimensions (width, thickness, diameter, twist, and straightness)
- surface quality
- corner radius
- rhomboidity
- compression test
- crack investigations
- steel mechanical parameters evaluation
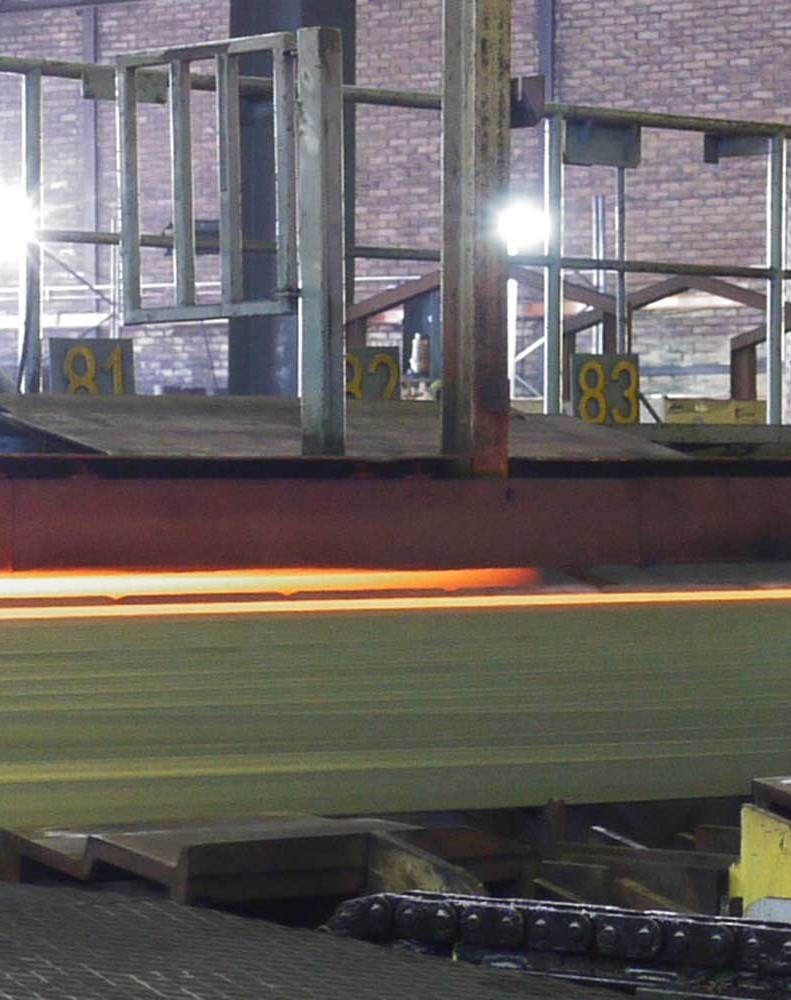
Packing device (Stacker)
The stacker is positioned between the cold shear and the binding area. It receives the already cut bars and assemble them neatly through a chain transfer and a packing system.
The layers of bars are collected by a lifting electromagnets and positioned on a mobile packing bench. The neatly packed bundle is then moved via a roller table to the binding area.

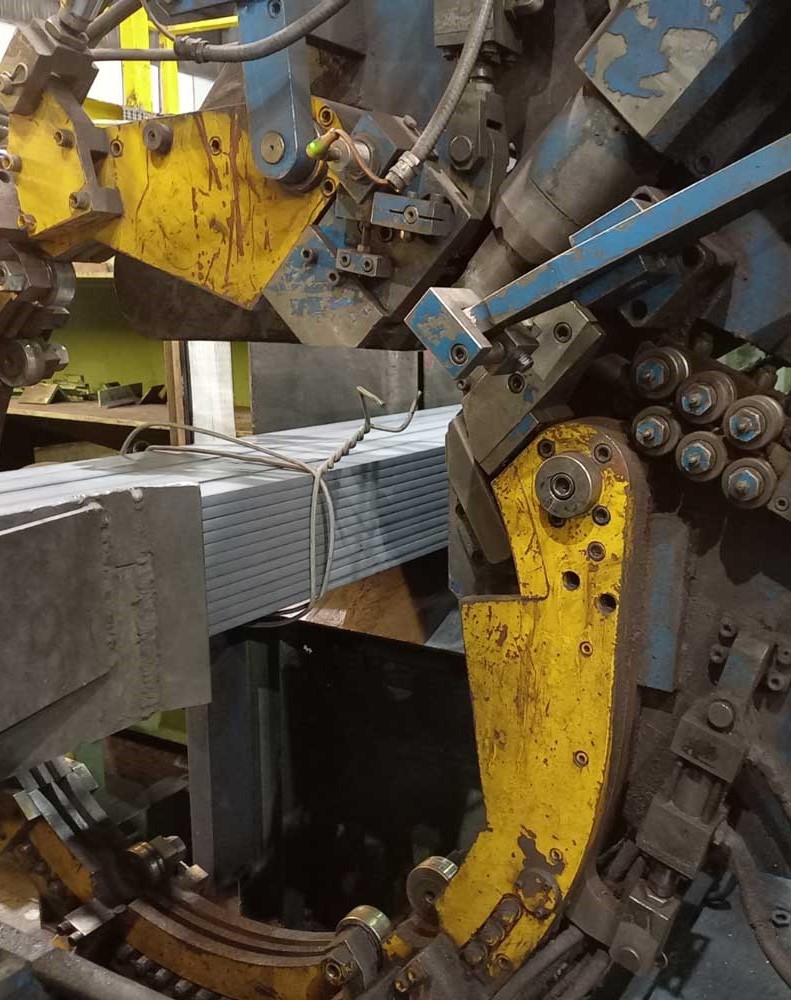
Binding machines
Packed bundle is transferred to the set of binding machines by means of a roller table to be bound with a steel wire or a steel strap.
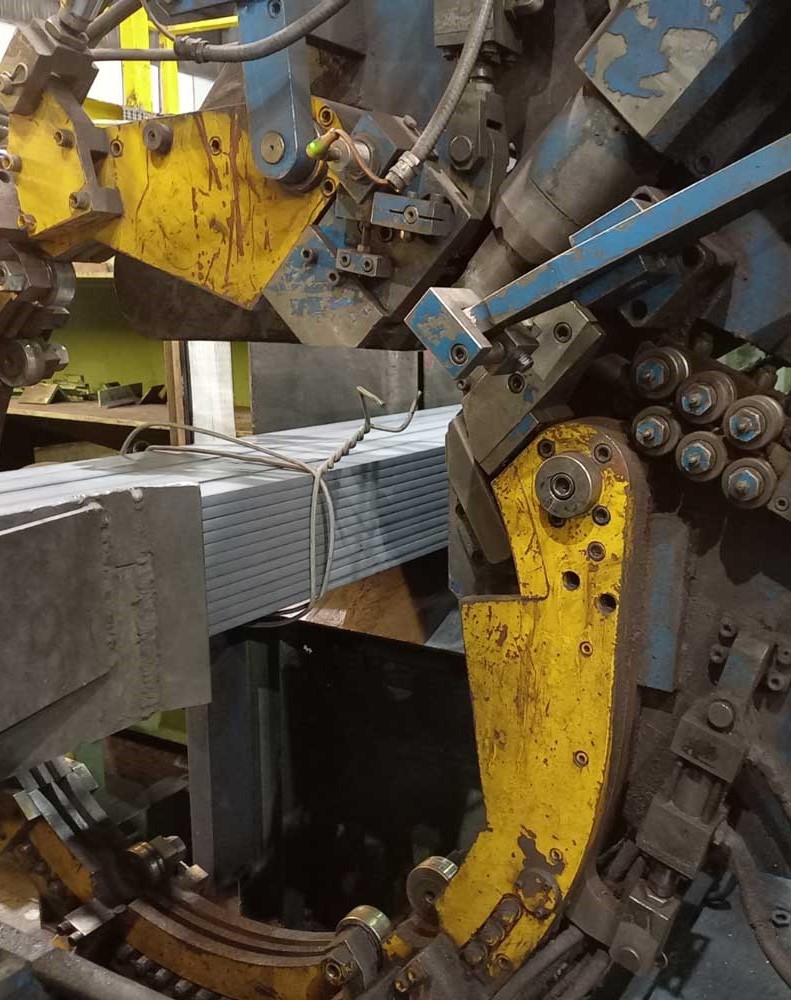
Labeling station
Label is attached to the finished bundle and moved over to the storage area.
The label contains next critical information:
- Size and quality of the steel
- Heat number
- Weight of the bundle
- Additional information as per order request
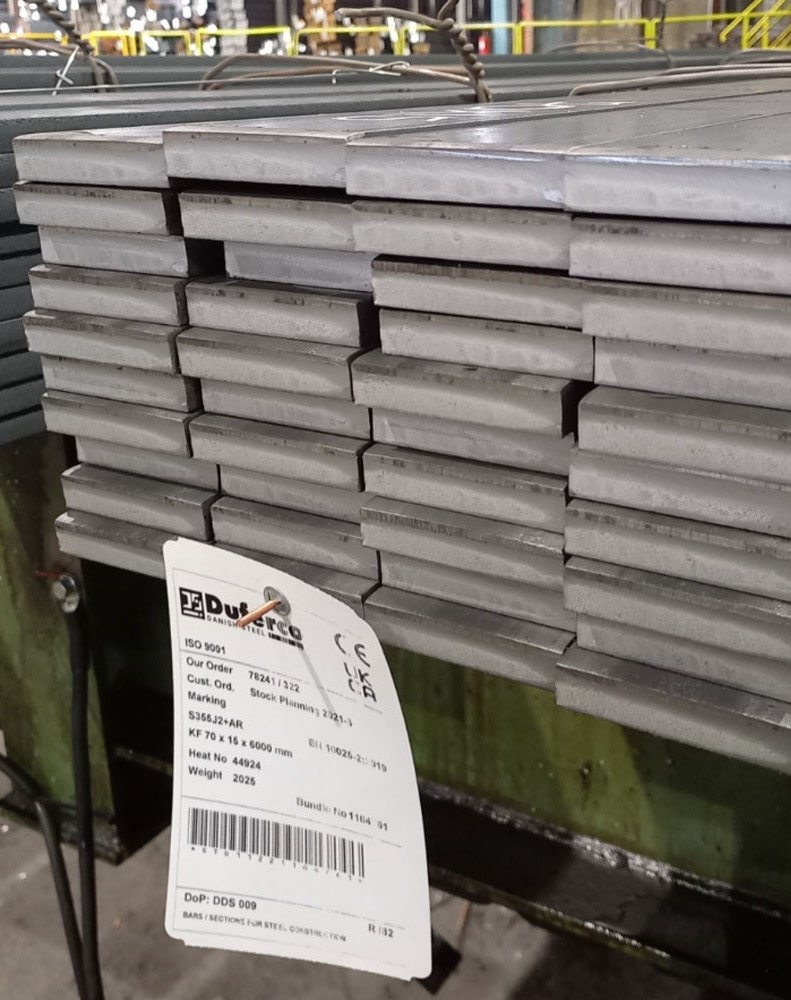
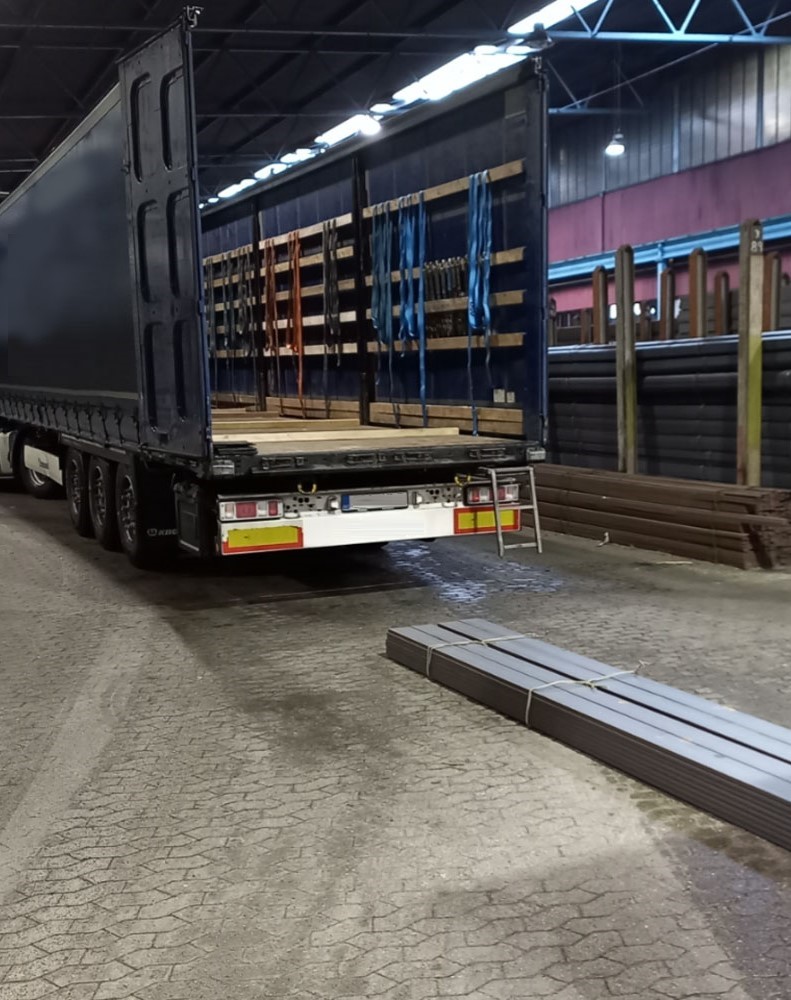
Packaging and Shipping
The bundles are opened if necessary, and a closer inspection (visual or measuring) of the single bars are done. The bundles are loaded in lorries or ships.
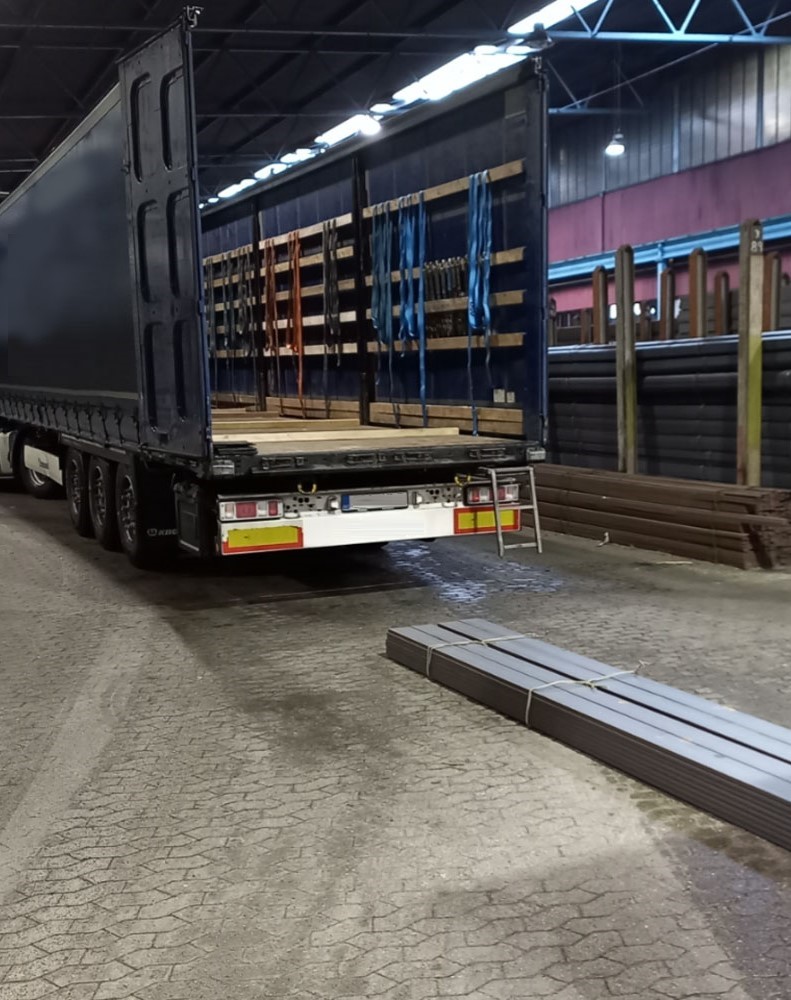